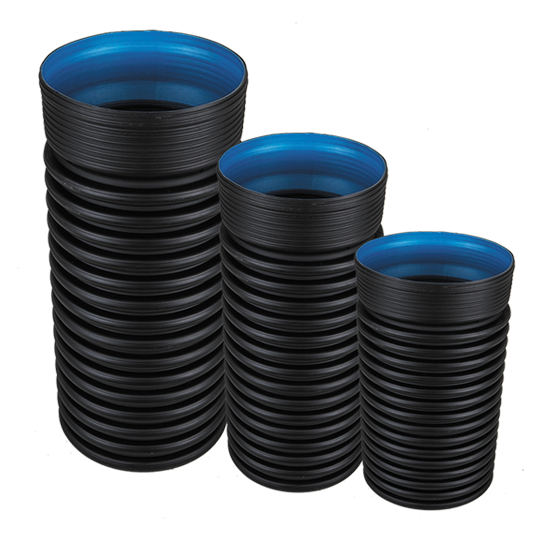
GENERAL FEATURES OF CORRUGATED PIPE
It is produced in SN4 and SN8 classes according to TS EN 13476-1 and DIN 16961-16566 standards, between Ø100 and 800 diameters. It does not require extra sleeves and saves labor because it is self-muffed in all diameters. Since it is produced from polyethylene raw material; It is an ideal product for long-lasting sewage systems with corrosion resistance, high wear resistance and excellent chemical resistance. Sewer pipes are a product produced from Polypropylene and Polyethylene raw materials in the Polyolefin group. Extruded corrugated pipes produced up to Ø1000 mm diameter can be produced from polyethylene and polypropylene raw materials, while spiral corrugated pipes are produced from polyethylene. Since the ring strength value is higher in polypropylene at the same wall thickness, it is more preferred. By the spiral method, pipes with a diameter of Ø300 mm and above are produced.
Injection fittings are produced for joining extruded corrugated pipes. Gaskets are placed in the channel on the outer surface of the pipe and inserted into the fitting. Spiral corrugated pipes can be joined by electrofusion method as well as extruder welding sealed method. This joining method makes pipes that are normally used under 0.5 bar pressure usable even at 4 bar.
In this way, the pipes continue to operate without leaking and without being damaged at the joints in case of pressure increases encountered in precipitation that turns into floods.
Since the corrugated pipes are not affected by corrosion and have high abrasion and chemical resistance, they are sold with a lifetime guarantee of 50 years. Thanks to their flexible structures, they carry out their activities without being affected by ground shaking such as earthquakes.
Since the impermeability is ensured throughout the life of the pipe, contamination of groundwater and soil is prevented. It is out of question for tree roots to enter the pipe and close. With its light weight, it can be installed in small diameter pipes without the need for a construction machine.
CORRUGATED PIPE AREAS OF USE AND BASIC FEATURES
It shows high resistance to abrasion and excellent resistance to chemicals.
It is desirable that the pipe materials used in sewage systems are not corroded and resistant to chemicals. Aggressive chemicals found both in the wastewater and in the soil have damaged the pipe material in the existing sewerage networks. Since polyethylene raw material is a corrosion resistant material, it is the ideal pipe material for long-lasting sewer systems. It can also be used for the storage and transfer of chemicals.
EASE OF STORAGE AND TRANSPORTATİON WİTH TELESCOPIC STACKING
Corrugated pipes are very light and at the same time resistant to impacts. There is no wastage during transportation and stocking. Since its light, it can be easily put into each other and stocked or transported.
EASY JOINING METHODS
Corrugated pipes can be combined with a bush gasket or with a sleeve gasket. Head fastening can be done easily in any construction site environment. Due to its lightness in all kinds of horizontal-vertical transportation at the construction site, the need for construction equipment is minimal.
EASE OF LAYING
Since the corrugated pipe is light, heavy equipment is not needed during laying. Thanks to its easy joining methods, the laying speed is higher than other pipe materials. It is a pipe material used especially in urban construction sites and in areas where the construction season is short.
SEALING
Sealing is provided up to a pressure of 0.5 bar in systems where the jointing method with muffle seal and sleeve seal is applied. In this way, sewage wastes do not mix with groundwater and our environment is protected. In addition, in places with high ground water, the entry of water from the outside into the sewer system is prevented. This prevents the line from overfilling and overflowing.
LONG-LASTING LIFETIME
The design life of corrugated pipes is minimum 50 years. For this reason, operation and maintenance costs are minimal.
SMOOTH FLOW SURFACE
Since the hydraulic roughness of corrugated pipes is very low compared to other pipe materials, a lower diameter can be selected and used by optimizing the diameter in the sewer system.In this way, the project cost of laying at the construction site can be reduced compared to the concrete pipe. In addition, the smooth surface prevents the solid particles in the system from adhering to the inner surface of the pipe and the narrowing of the cross-section that may occur over time is prevented.
FLEXIBLE
Since corrugated pipes are flexible, they adapt to ground movements and do not deform.
During the production of the desired length, breakage and losses are zero.Muffed pipes are produced in standard 6 m lengths. Pipes without bell can be produced in the desired length according to customer demand. Relevant standards Pr-En 13476 -1, CEN/TC 155WI 011
ADVANTAGES OF CORRIGATED PIPES
• It has a service life of 50 years.
• It preserves the natural properties of water and is hygienic.
• It can be produced as coil and length. It provides very fast line laying opportunity especially in coil pipes.
• On curved terrains due to its flexibility (it can be bent up to 18-50 times the pipe diameter depending on the wall thickness [it is easy and economical], it provides less elbow usage).
• It adapts to soil movements such as earthquakes and landslides.
• Offers safe and practical connection solutions.
• Modern laying techniques can be applied.
• Provides high resistance to chemicals, does not corrode.
• It is not affected by sunlight thanks to its UV additive.
• Due to the smooth inner surface of the pipe, the particles in the fluid cannot adhere to the inner surface of the pipe and there is no time-dependent cross-sectional narrowing. Provides higher flow rate.
• It does not hold algae on the inner surface of the pipes and does not produce bacteria.
PRODUCTION FEATURES
There are two different production methods of corrugated pipes. They are produced in a continuous, single process extruder and on the mandrel with the helical method. The production capacity of extruded corrugated pipes is very high, and the ring strength value is constant since the shape of the product cannot be changed. Helical corrugated pipes, on the other hand, can be produced at the desired ring strength value and optimum weight depending on the project.The pipes consist of two layers, the inner tube layer and the outer rib layer. The inner layer is a flat-walled pipe that carries the fluid. The outer layer is ribbed. Both layers are molecularly linked to each other. Since the outer hollow rib structure can carry loads (close to the full structure) due to the laws of physics, it is preferred for saving raw materials and reducing the weight of the pipe.
Extruded corrugated pipes come out of the extruder in two layers and the outer layer is shaped by molds.In the spiral corrugated pipe, first the inner pipe is turned into a pipe by wrapping the polyethylene in the form of strips on top of each other in the mandrel.Afterwards, the product drawn as a profile is wrapped on the pipe and welded. Both products show a monolithic feature with their welded structure.
THINGS TO PAY ATTENTION
When filling the channel, compaction should be done layer by layer so that there is no space around the pipes. In particular, it should be ensured that the bottom of the pipe is filled with filling material. If the filling is done by compressing well according to the specification, the traffic and soil load coming to the pipe are transferred to the filling, so the pipe fulfills its duty throughout its lifetime. Otherwise, when there is a gap, the pipe carries what it can carry, and collapses when it cannot find a place to transfer the forces above it. The same is true for steel pipes.In gasketed systems, lubricants such as soap and silicone should be used to allow the pipes to enter the fitting. Before electrofusion welding, it should be checked that the surfaces are clean. Before welding, care should be taken that the wires do not touch each other.
Our ISIN PP-R Pipes carries the advantageous aspects of the plastic pipe industry such as; smooth, shiny, hygienic and easy installation. It is an indispensable
solution for hot water systems as opposed to indoor and cold galvanized pipes. PP-R Pipes are used safely in shopping mall, airport, municipality and public buildings, residence, villa, subway, school, hotel and stadium projects.
All kinds of PP-R Pipes and Fittings used for the stages of hot and cold water installations in buildings are
producing from the highest quality raw materials. PP-R raw material is divided into three classes in terms of heat, pressure and chemical durability. These are: Type-1, Type-2 and Type-3. Raw material PP-H (Polypropylene Homopolymer), Type-2,
Raw material PP-B (Polypropylene Blockcopolymer), Type-3, Raw material PP-R (Polypropylene Randomcopolymer), includes Type-1 PP-H. Type-3 raw material
has higher performance and better properties in terms of physical and chemical properties of Type-1 and Type-2 raw materials. The most important feature of this raw material in the PP-R pipe industry is its high resistance to heat and chemical hazards. The reason for the successful use of PP-R Pipes and Fittings in cold and hot water systems is due to the resistance of the raw material of PP-R. The monomer
structure of PP-R raw material creates a random chain and protects it. PP-R Pipe and Fittings It does not allow any biological material that produces the raw material of PP-R, it can be colored, and provides excellent properties in preserving the taste and smell of the fluid passing through it.
PP-R FIBER GLASS PIPES AND FITTINGS
Glass Fiber Composite Pipe consists of 3 layers. The inner and outer layers are made of polypropylene (PP-R), and the intermediate layer is composed of glass
fiber and PPR raw material.Glass Fiber Composite Pipe, which is formed by combining the advantages of straight pipes and foiled pipes, provides high
efficiency and usage advantages and eliminates many disadvantages such as shaving.
FEATURES
• Does not require shaving. Therefore, it provides faster assembly and application possibilities.
• There is no sweating and elongation problem.
• It can be used as an alternative to foiled pipes as it has an expansion coefficient close to the foiled pipes. Its working life is 50 years at 20 C and 20 bar pressure.
• Since they have a low expansion coefficient, they can be used in the temperature range
of -20 to 95 C. (However, insulation should be applied considering the
freezing point of the fluid in the pipe at minus degree.)
• It is resistant to freezing in cold weather. However, appropriate insulation
should be applied considering the freezing degree of the fluid in the pipe.
• It does not cause any change in the color, smell and taste of the water. It is environmentally friendly.
INSTALLATION
If the ambient temperature is below +5C, the heating time should be increased by 50%. This time is the time from the removal of the pipe and fitting from the welding threads to the joint. After the installation of the composite pipe installation is completed, the quality control of the installation must be carried out by applying the following test procedure. All valves in the installation are brought to the closed position. While the installation is being filled, the main valve is
slightly opened first. In order to avoid strong pressure pulses, the air is carefully taken from the highest and farthest usage area of the pipelines. While testing, the valve of each zone should be opened separately.
Step 1: The entire piping system in the building is subjected to a leak test for 30 minutes at 1.5 times the maximum prescribed pressure. Pressure drop and
leakage are observed between the 10th and 20th minutes. The pressure is raised again. During the 30-minute period, a pressure drop of more than 0.6 bar and leakage should not occur at any point.
Step 2: A pressure of 1.5 times is applied for 2 hours. This time, a pressure drop of more than 0.2 bar and leakage should not occur at any point of the installation.
If the pressure drops more than the values given above in the manometer
where the test is being monitored, there is a leak. Leaking pipeline should be checked and
replaced or re-tightened. All installations should be washed before starting to use. Lines that will not be used should be closed and drained against freezing.
SIGNIFICANT MATTERS IN PP-R COMPOSITE PIPES AND FITTINGS
At the end of the foil peeling process in PP-R pipes with aluminum foil, there should be absolutely no foil particles in the welding distance.For turns over 30º, a 45º
elbow should be used.Excessive tightening should be avoided in metal fitting applications, teflon tape should be used instead of hemp.Pipes should be cut perpendicular
to the pipe axis and with sharp pipe cutters.Dirty pipes and fittings should not be welded, deformed and cracked pipes and fittings should not be used.Pipes must be protected from all kinds of impact and impact.Conical threaded parts should not be used in the connections.The installation must be protected against the risk of freezing.If the installation will not be used after the test process, the water in the installation must be emptied against the risk of freezing.Welding should not be done if the Teflon on the threads is worn out or broken. (Teflon life is as long as 2-3 residential applications.)Welding waiting time should be observed, pipes and fittings should not be rotated during melting.Precautions should be taken against steam compression in gas water heater installations.Pipe and fittings should not be exposed to direct sunlight for a long time.PP-R raw material does not contain UV-resistance stabilizer. The maximum storage period is six months in the environment in contact with sunlight.After the installation is laid, the pipes and fittings in the sections outside the building should be isolated against UV rays and freezing.
Our ISIN PP-R Pipes carries the advantageous aspects of the plastic pipe industry such as; smooth, shiny, hygienic and easy installation. It is an indispensable
solution for hot water systems as opposed to indoor and cold galvanized pipes. PP-R Pipes are used safely in shopping mall, airport, municipality and public buildings, residence, villa, subway, school, hotel and stadium projects.
All kinds of PP-R Pipes and Fittings used for the stages of hot and cold water installations in buildings are
producing from the highest quality raw materials. PP-R raw material is divided into three classes in terms of heat, pressure and chemical durability. These are: Type-1, Type-2 and Type-3. Raw material PP-H (Polypropylene Homopolymer), Type-2,
Raw material PP-B (Polypropylene Blockcopolymer), Type-3, Raw material PP-R (Polypropylene Randomcopolymer), includes Type-1 PP-H. Type-3 raw material
has higher performance and better properties in terms of physical and chemical properties of Type-1 and Type-2 raw materials. The most important feature of this raw material in the PP-R pipe industry is its high resistance to heat and chemical hazards. The reason for the successful use of PP-R Pipes and Fittings in cold and hot water systems is due to the resistance of the raw material of PP-R. The monomer structure of PP-R raw material creates a random chain and protects it. PP-R Pipe and Fittings It does not allow any biological material that produces the raw material of PP-R, it can be colored, and provides excellent properties in preserving the taste and smell of the fluid passing through it.
PP-R FIBER GLASS PIPES AND FITTINGS
Glass Fiber Composite Pipe consists of 3 layers. The inner and outer layers are made of polypropylene (PP-R), and the intermediate layer is composed of glass
fiber and PPR raw material.Glass Fiber Composite Pipe, which is formed by combining the advantages of straight pipes and foiled pipes, provides high
efficiency and usage advantages and eliminates many disadvantages such as shaving.
FEATURES
• Does not require shaving. Therefore, it provides
faster assembly and application possibilities.
• There is no sweating and elongation problem.
• It can be used as an alternative to foiled pipes as
it has an expansion coefficient close to the foiled pipes. Its working life is
50 years at 20 C and 20 bar pressure.
• Since they have a low expansion coefficient, they can be used in the temperature range
of -20 to 95 C. (However, insulation should be applied considering the
freezing point of the fluid in the pipe at minus degree.)
• It is resistant to freezing in cold weather. However, appropriate insulation
should be applied considering the freezing
degree of the fluid in the pipe.
• It does not cause any change in the color, smell and
taste of the water. It is environmentally friendly.
INSTALLATION
If the ambient temperature is below +5C, the heating time should be increased by 50%. This time is the time from the removal of the pipe and fitting from the welding threads to the joint. After the installation of the composite pipe installation is completed, the quality control of the installation must be carried out by applying the following test procedure. All valves in the installation are brought to the closed position. While the installation is being filled, the main valve is
slightly opened first. In order to avoid strong pressure pulses, the air is carefully taken from the highest and farthest usage area of the pipelines. While testing, the valve of each zone should be opened separately.
Step 1: The entire piping system in the building is subjected to a leak test for 30 minutes at 1.5 times the maximum prescribed pressure. Pressure drop and
leakage are observed between the 10th and 20th minutes. The pressure is raised again. During the 30-minute period, a pressure drop of more than 0.6 bar and leakage should not occur at any point.
Step 2: A pressure of 1.5 times is applied for 2 hours. This time, a pressure drop of more than 0.2 bar and leakage should not occur at any point of the installation.
If the pressure drops more than the values given above in the manometer
where the test is being monitored, there is a leak. Leaking pipeline should be checked and
replaced or re-tightened. All installations should be washed before starting to use. Lines that will not be used should be closed and drained against freezing.
SIGNIFICANT MATTERS IN PP-R COMPOSITE
PIPES AND FITTINGS
At the end of the foil peeling process in PP-R pipes with aluminum foil, there should be absolutely no foil particles in the welding distance.For turns over 30º, a 45º
elbow should be used.Excessive tightening should be avoided in metal fitting applications, teflon tape should be used instead of hemp.Pipes should be cut perpendicular
to the pipe axis and with sharp pipe cutters.Dirty pipes and fittings should not be welded, deformed and cracked pipes and fittings should not be used.Pipes must be protected from all kinds of impact and impact.Conical threaded parts should not be used in the connections.The installation must be protected against the risk of freezing.If the installation will not be used after the test process, the water in the installation must be emptied against the risk of freezing.Welding should not be done if the Teflon on the threads is worn out or broken. (Teflon life is as long as 2-3 residential applications.)Welding waiting time should be observed, pipes and fittings should not be rotated during melting.Precautions should be taken against steam compression in gas water heater installations.Pipe and fittings should not be exposed to direct sunlight for a long time.PP-R raw material does not contain UV-resistance stabilizer. The maximum storage period is six months in the environment in contact with sunlight.After the installation is laid, the pipes and fittings in the sections outside the building should be isolated against UV rays and freezing.
Our ISIN PP-R Pipes carries the advantageous aspects of the plastic pipe industry such as; smooth, shiny, hygienic and easy installation. It is an indispensable
solution for hot water systems as opposed to indoor and cold galvanized pipes. PP-R Pipes are used safely in shopping mall, airport, municipality and public buildings, residence, villa, subway, school, hotel and stadium projects.
All kinds of PP-R Pipes and Fittings used for the stages of hot and cold water installations in buildings are
producing from the highest quality raw materials. PP-R raw material is divided into three classes in terms of heat, pressure and chemical durability. These are: Type-1, Type-2 and Type-3. Raw material PP-H (Polypropylene Homopolymer), Type-2,
Raw material PP-B (Polypropylene Blockcopolymer), Type-3, Raw material PP-R (Polypropylene Randomcopolymer), includes Type-1 PP-H. Type-3 raw material
has higher performance and better properties in terms of physical and chemical properties of Type-1 and Type-2 raw materials. The most important feature of this raw material in the PP-R pipe industry is its high resistance to heat and chemical hazards. The reason for the successful use of PP-R Pipes and Fittings in cold and hot water systems is due to the resistance of the raw material of PP-R. The monomer
structure of PP-R raw material creates a random chain and protects it. PP-R Pipe and Fittings It does not allow any biological material that produces the raw material of PP-R, it can be colored, and provides excellent properties in preserving the taste and smell of the fluid passing through it.
PP-R FIBER GLASS PIPES AND FITTINGS
Glass Fiber Composite Pipe consists of 3 layers. The inner and outer layers are made of polypropylene (PP-R), and the intermediate layer is composed of glass
fiber and PPR raw material.Glass Fiber Composite Pipe, which is formed by combining the advantages of straight pipes and foiled pipes, provides high
efficiency and usage advantages and eliminates many disadvantages such as shaving.
FEATURES
• Does not require shaving. Therefore, it provides faster assembly and application possibilities.
• There is no sweating and elongation problem.
• It can be used as an alternative to foiled pipes as it has an expansion coefficient close to the foiled pipes. Its working life is 50 years at 20 C and 20 bar pressure.
• Since they have a low expansion coefficient, they can be used in the temperature range
of -20 to 95 C. (However, insulation should be applied considering the
freezing point of the fluid in the pipe at minus degree.)
• It is resistant to freezing in cold weather. However, appropriate insulation
should be applied considering the freezing degree of the fluid in the pipe.
• It does not cause any change in the color, smell and taste of the water. It is environmentally friendly.
INSTALLATION
If the ambient temperature is below +5C, the heating time should be increased by 50%. This time is the time from the removal of the pipe and fitting from the welding threads to the joint. After the installation of the composite pipe installation is completed, the quality control of the installation must be carried out by applying the following test procedure. All valves in the installation are brought to the closed position. While the installation is being filled, the main valve is
slightly opened first. In order to avoid strong pressure pulses, the air is carefully taken from the highest and farthest usage area of the pipelines. While testing, the valve of each zone should be opened separately.
Step 1: The entire piping system in the building is subjected to a leak test for 30 minutes at 1.5 times the maximum prescribed pressure. Pressure drop and
leakage are observed between the 10th and 20th minutes. The pressure is raised again. During the 30-minute period, a pressure drop of more than 0.6 bar and leakage should not occur at any point.
Step 2: A pressure of 1.5 times is applied for 2 hours. This time, a pressure drop of more than 0.2 bar and leakage should not occur at any point of the installation.
If the pressure drops more than the values given above in the manometer
where the test is being monitored, there is a leak. Leaking pipeline should be checked and
replaced or re-tightened. All installations should be washed before starting to use. Lines that will not be used should be closed and drained against freezing.
SIGNIFICANT MATTERS IN PP-R COMPOSITE PIPES AND FITTINGS
At the end of the foil peeling process in PP-R pipes with aluminum foil, there should be absolutely no foil particles in the welding distance.For turns over 30º, a 45º
elbow should be used.Excessive tightening should be avoided in metal fitting applications, teflon tape should be used instead of hemp.Pipes should be cut perpendicular
to the pipe axis and with sharp pipe cutters.Dirty pipes and fittings should not be welded, deformed and cracked pipes and fittings should not be used.Pipes must be protected from all kinds of impact and impact.Conical threaded parts should not be used in the connections.The installation must be protected against the risk of freezing.If the installation will not be used after the test process, the water in the installation must be emptied against the risk of freezing.Welding should not be done if the Teflon on the threads is worn out or broken. (Teflon life is as long as 2-3 residential applications.)Welding waiting time should be observed, pipes and fittings should not be rotated during melting.Precautions should be taken against steam compression in gas water heater installations.Pipe and fittings should not be exposed to direct sunlight for a long time.PP-R raw material does not contain UV-resistance stabilizer. The maximum storage period is six months in the environment in contact with sunlight.After the installation is laid, the pipes and fittings in the sections outside the building should be isolated against UV rays and freezing.
First of all, the recommended welding machine and apparatus
should be used, welding instructions should be followed. It is necessary to
check that the temperature of the heater machine is working at the ideal
temperature. For this, a temperature measuring instrument or a temperature
measuring pen can be used. If the color of the pen with an orange tip turns
gray on the hot sheet, the temperature is at the ideal level. Before welding,
it should be checked whether the threads are clean, and if necessary, they
should be cleaned with a wet or alcohol cloth.
PVC Sewage Water Pipes and Fittings are used in villas and multi-storey residences, hospitals, schools, hotels, industrial and sportive etc. Being ecological and economical in buildings and preserving its physical structure up to 60ºC, they ensure that the building foundation and indoor sewage water is discharged through PVC pipes in an ideal and safe way without leaking, for long-term use. Thanks to its smooth, bright inner and outer surfaces, there is no sediment and accumulation in the sewage water installation, no bacteria, odor, clogging and flow performance loss. No flaking or peeling occurs on the pipe surfaces. ISIN PVC sewage waste water pipes and fittings, produced from hard PVC raw material, which ‘difficult flammable building material’ class defined as B1 in DIN 4102 standards and National Fire Regulations. ISIN PVC-based Sewage Water Pipes and Fittings do not catch fire easly and do not allow the passage of fire between floors. PVC sewage water
pipes and fittings are absolutely leak-proof thanks to their "o-ring" gasket and fully compatible gasket seat. Thanks to its easy attachment and detachment, the evacuation system can be assembled quickly and without cutting, bending, gluing, etc. does not requires grueling work. The sewage water discharge system made of ISIN PVC pipes and fittings successfully meets the sealing performance test. This test performed by giving water to the system for 15 minutes while bar pressure 0.5. ISIN PVC Sewage Water Pipes and Fittings have 50 to 315 mm diameter 150 to 6000 mm length options it provides any kind of need about water drainage. Production is made in SO type according to TS 275-1 EN 1329-1 standard.
SO type sewage water pipes are used inside and outside the buildings to suitable
distance to wall or under the ground.
STORAGE AND OPERATING
Products should be stored at tropical temperatures, flat and free from sharp stones or piles, to a maximum height of 1.5 meters with sockets at alternate ends on
75 mm square timber on 1.5 meters centres.
U-PVC is a
tough and flexible material, but careless handling can cause damage. Extra care
is required in very hot or cold conditions. ISIN PVC Sewage Water Pipes and
Fittings can be easily stacked on top of each other and telescopically thanks
to their rigid feature, thus providing advantages in stocking and
transportation.
TSE PPR CERTIFICATE
DOMESTIC GOODS CERTIFICATE
TSE PVC CERTIFICATE
TSE CORRUGE CERTIFICATE
ISO CERTIFICATE
WARRANTY CERTIFICATE
© 2021 AIP Export. All Rights Reserved. AOSB